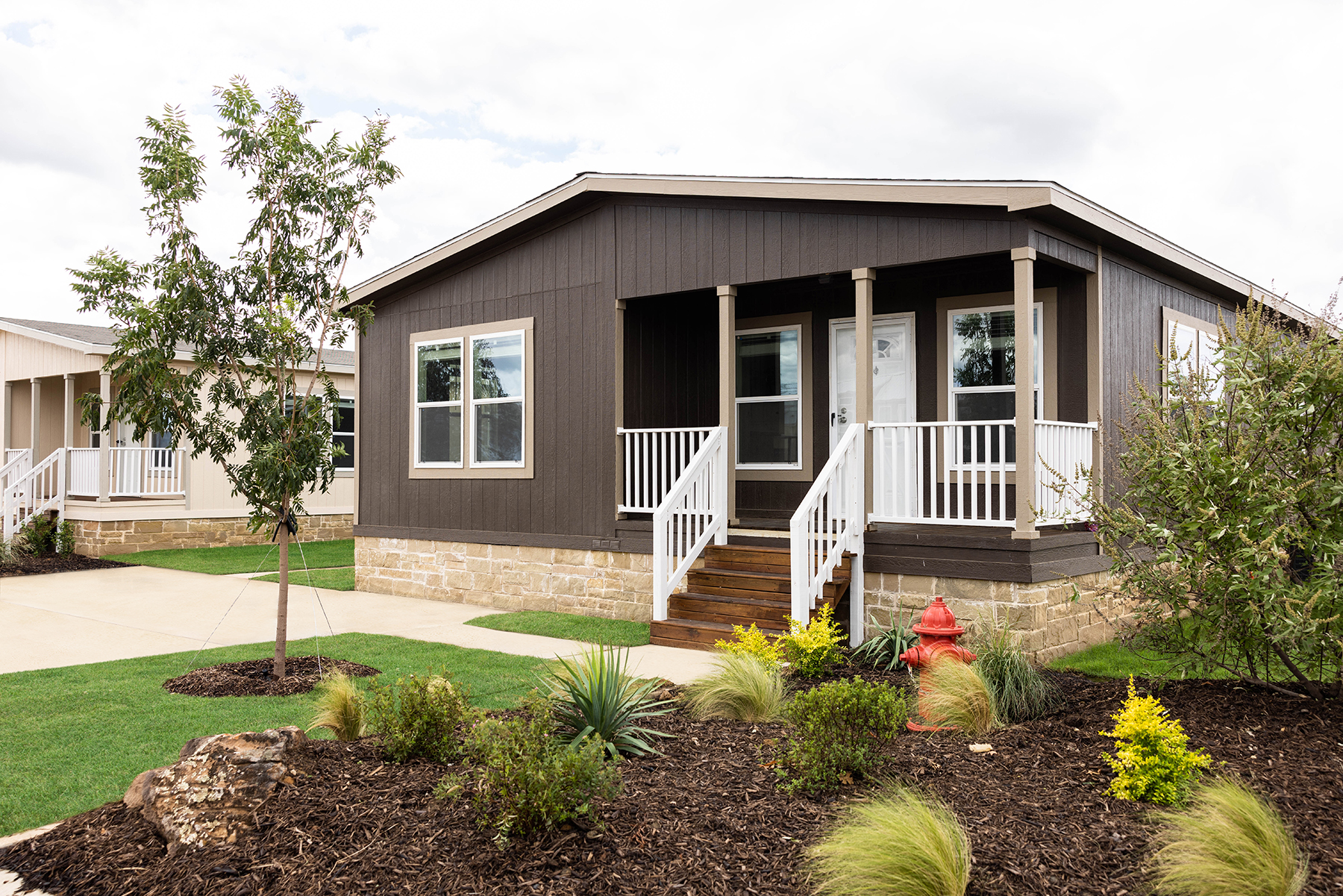
Off-site homes
There are more similarities than differences between "off-site" built homes (often referred to as manufactured homes) and "site-built" homes (homes built on site).
Many site-built homes have peer-and-beam foundations. This is when concrete beams are used on the perimeter and major supporting mid-lines, with peers spaced throughout. Then floor joists, also known as beams, are laid across the peers and span across the entirety of what will become the floor of the house. Then flooring is laid on top of the peers and beams. Once the floor is down, wall framing is built with two by four lumber. After framing, the exterior is wrapped, and exterior siding is installed. Trusses make up the roof support system, also made out of two by four – or sometimes two by six – lumber, which then get sheathed with plywood, covered with underlayment (often tar paper), and finished with shingles.
Once the home has been weather sealed, the interior infrastructure, such as electrical and water lines, is installed. Insulation is installed between framing. Then sheetrock is installed on the interior once the infrastructure is completed. Tape and mud are applied to cover and hide seams between sheets of sheetrock. Doors and windows are installed. Texture and paint are applied. Flooring is installed. Any trim out, such as baseboards and crown molding, are installed. Appliances are installed. And pending any final finishing items, the home is completed.
Off-site homes are nearly identical. The only differences are:
- They are built in controlled environments where they are shielded from weather elements like sun and rain.
- The foundation beams are made out of steel instead of concrete.
- They are built off-site and then transported to where they will live.
efficient construction
The off-site construction process has many benefits over the site-built process.
- The same people are building the homes. And because of this, they get really good at what they are doing and are able to focus on the details. They spend more time building and less time traveling from job site to job site.
- Leftover and scrap materials are able to be used on the next house instead of getting tossed in a dumpster and ending up in a landfill. Thus reducing waste and added material costs.
- The off-site process require frequent facilities inspections and code enforcement. Maintaining all of this in one place, standards of construction are more readily overseen and upheld.
- Because the homes are sold as a unit, there are no individual inspections like you would experience with site-built homes. This means less time getting a completed home to where it will live.
quality materials
Two by four framing. Three-quarter inch sheetrock. Thirty year shingles. Standard insulation. These are residential homes. We select manufactures that use the same high quality materials that are used in most site-built homes. They are built to last. This means you will be able to be confident in your purchase, knowing it will be able to withstand decades of life for you and your family.
Beyond just the homes themselves, we pave all of the roads in our communities with concrete and asphalt. No dirt roads here. Parking areas are painted with striping to indicate parking spaces, fire lanes, and more. We want you to truly live in luxury when you move into a First Step Homes community.
experience the SFO difference
providing attainable single-family ownership
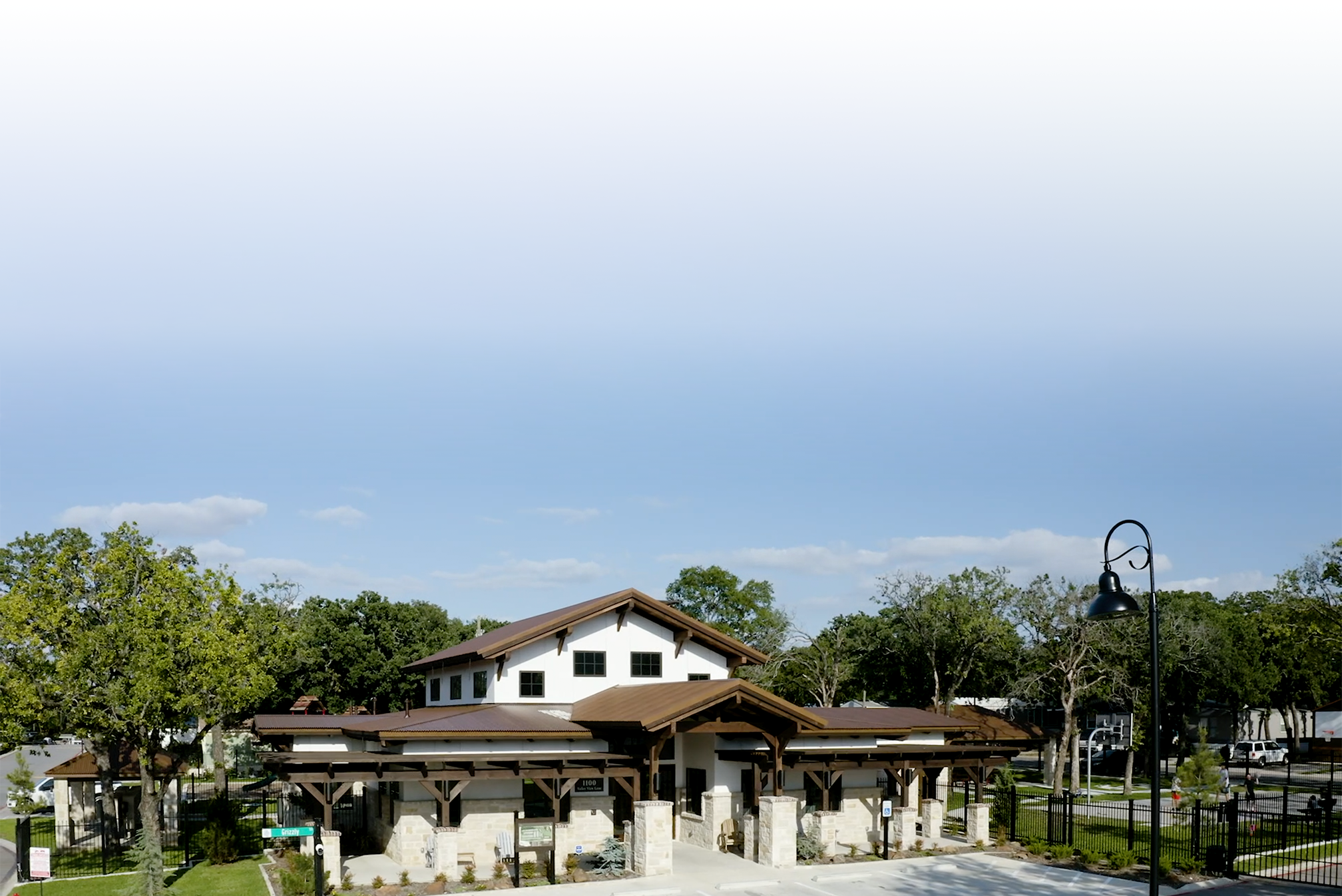